Toyota Motors Value Chain
The value chain is a representation of the internal activities that a firm engages in to transform inputs into outputs. The firms use value chain analysis as a tool to analyze these internal activities and determine their value. The firms are able to identify the activities that require improvement to create a competitive advantage. Toyota’s value chain steps include support and primary activities (Ball, Love, & Albores, 2008). The support activities include firm infrastructure, HR, development of technology, and procurement. The primary activities include inbound logistics, operations, outbound logistics, marketing, and sales, as well as service.
Toyota’s main sub-processes include mix planning, forecasting, scheduling of production, dealer allocation, parts ordering, and inbound logistics planning. The mix planning process entails limiting each vehicle’s specifications that have been ordered in each market for stock. The specifications are divided into factory-installed, color, and accessories. The mix planning is done annually and adjusted as the need arises to reflect the trends in demand. Using the first month’s order, Toyota’s sales division is able to provide a forecast for the next two months. This data is used to create a production schedule, which guides the company’s activities. The production schedule relies on the heijunka principle, which enables the smoothing of specific aspects over others. Dealers receive allocations based on the characteristics that they have in each vehicle. Ordering parts for both local and overseas parts is done. This process is connected to logistics, where determinations regarding the ideal routes to use when picking up parts from suppliers are done (Iyer, Seshadri, & Vasher, 2009). Each of these processes is connected to the other and determines the company’s success in the transformation of inputs into outputs.
To analyze the effectiveness of a process, Toyota would need to consider its ability to satisfy the projected demand, fulfill the required quality, and maintain reasonable costs of production. The process of fulfilling demands from clients entails planning and logistics. If one of the sub-processes is affected negatively by expected or unexpected circumstances, it is likely to spread the impact through the entire organization (Iyer, Seshadri, & Vasher, 2009). For instance, a crisis is one of the elements that can test the supply chain’s effectiveness. If Toyota, during a crisis, is unable to order parts overseas, such a situation is likely to lead to innovative ideas regarding the most efficient methods of sourcing the same parts elsewhere. This action fail-proofs the entire supply chain. Other metrics that can be used to evaluate the supply chain include lead times, the ability to respond to changes, and stock levels (Ball, Love, & Albores, 2008).
Toyota’s cases of overproduction and underproduction affected the entire chain. Forecasting demand ahead of time is a challenging aspect of the company’s production process. The company used the ‘sell one, buy one’ tactic. Toyota implemented a separation of orders’ cut-off times based on the delivery route. Orders were processed, packed, and shipped/picked up immediately after the cut-off times elapsed. The replenishment of stock daily led to a decrease in critical orders from 30 percent to between 1 and 3 percent. The receipt period was reduced to an average of 14 hours. The aspects also affected suppliers positively because they reduced the inventory supply to 35 days and increased the stock of various part numbers by 50 percent. Improving the efficiency of suppliers and delivery performance resulted in increased productivity, which is one of Toyota’s competitive advantages (Sutherland & Bennett, 2007).
References
Ball, P., Love, D., & Albores, P. (2008). Financial Evaluation in Supply Chain Design using Enterprise Simulation.
Iyer, A. V., Seshadri, S., & Vasher, R. (2009). A Strategic Approach to the Principles of Toyota’s Renowned System. McGraw Hill.
Sutherland, J., & Bennett, B. (2007). The Seven Deadly Wastes of Logistics: Applying Toyota Production System Principles to Create Logistics Value. Retrieved from https://www.researchgate.net/publication/265356600_The_Seven_Deadly_Wastes_of_Logistics_Applying_Toyota_Production_System_Principles_to_Create_Logistics_Value
ORDER A PLAGIARISM-FREE PAPER HERE
We’ll write everything from scratch
Question
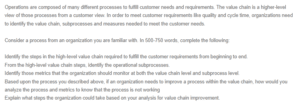
Toyota Motors Value Chain
Operations are composed of many different processes to fulfill customer needs and requirements. The value chain is a higher-level view of those processes from a customer view. In order to meet customer requirements like quality and cycle time, organizations need to identify the value chain, subprocesses and measures needed to meet the customer needs.
Consider a process from an organization you are familiar with. In 500-750 words, complete the following:
Identify the steps in the high-level value chain required to fulfill the customer requirements from beginning to end.
From the high-level value chain steps, identify the operational subprocesses.
Identify those metrics that the organization should monitor at both the value chain level and subprocess level.
Based upon the process you described above, if an organization needs to improve a process within the value chain, how would you analyze the process and metrics to know that the process is not working
Explain what steps the organization could take based on your analysis for value chain improvement.