The Impact of Quality on Operations Management- Cost Control, Failure, and Organizational System Efficiency
An overwhelming body of research suggests a positive correlation between better quality management and positive organizational operations outcomes. Today’s business growth environment is characterized by increased rivalry compared to past decades. In today’s competitive business environment, organizations that prioritize quality are more likely to thrive due to increased customer demands.
A variety of cost failures affect operations management in a business setting. First, there are prevention costs that are incurred to prevent poor quality in products and services (Sower et AL., 2007). Secondly, there are appraisal costs used to audit the quality of services and goods to ensure that they align with the required quality standards. Internal failure costs occur when products and services do not align with customer needs, while external failure costs are associated with products that fail to meet client needs after delivery. Sower et al. (2007) recommend approaches that may be used to ensure quality is achieved to avoid future failure costs. The systematic process-based approach emerges as one of the most effective quality management approaches. This system relies on available data to ensure that processes conform to requirements to avoid future setbacks. Similarly, best-in-class performance ensures products align with quality requirements based on established benchmarks.
For instance, a construction company using total quality management is likely to attain higher profits and sales because it will not incur unnecessary cost failures. To avoid costs, such a firm may employ strategies such as asking their clients to check on project progress to ensure it aligns with their needs. Also, the company may benchmark similar ongoing or successfully completed projects to ensure quality standards are met. Overall, a focus on quality impacts operations since businesses employ continual improvement procedures and quality auditing which change services or product manufacturing processes.
Deming’s 14 Management Principles
Creating a Constancy of Purpose
According to Metri (2006), this concept underlines the need for businesses to commit to continual quality improvement in the long run. In terms of quality control, constancy of purpose entails defining clear quality goals and ensuring that every decision and activity matches the ultimate goal of enhancing product or service quality. A corporate philosophy is critical to achieving this objective.
New Philosophy Adoption
Creating a new philosophy entails moving from a short-term focus to a long-term focus. As globalization proliferates the business environment, firms should ditch traditional culture and adopt newer philosophies informed by cultural changes. For instance, the Japanese Toyota company has to consider cultural changes in the Western world where it derives its market.
Cessation of Dependence on Inspection to Achieve Quality
This means eliminating the need for mass inspection by integrating quality into the product from the start. Inspections are obsolete, ineffective, and expensive. It is too late to make adjustments to the quality of an item or service after it is released.
Stop Awarding Business on Price
Instead of awarding a business purely on price, it is necessary to decrease overall cost. The company should transition to a single supplier for every item, based on an ongoing relationship of loyalty and trust. Quality and pricing are inseparable.
Improve Constantly and Forever the System of Production and Service
There is a continual desire to enhance test methodologies and better understand how customers use and misuse products. Continuous process improvement can take several forms. For example, constant advancement in the production process is beneficial.
Institute Training
Management training should include all areas of the firm, from supplies to client demands, as well as the influence of process variation on what is done in the company. Management must appreciate the worker’s difficulties in doing his or her duties properly.
Institute Leadership
The goal of supervision should be to assist people, machines, and devices perform well. Management oversight and manufacturing employee supervision both require improvement. The leadership team should lead, not oversee.
Drive Out Fear
No one can perform at his best until he feels safe. Workers should not be scared to share their views. Fear causes poor performance and inflated statistics.
Eliminate Departmental Barriers
Collaboration and communication across departments are critical for successful quality control. Organizations should aim to reduce bottlenecks and encourage cross-functional collaboration. That will ensure that quality factors are included across the value chain.
Eliminate Numerical Targets
Instead of depending on arbitrary targets, firms should prioritize giving people what they require to accomplish quality goals. Quality control activities should be data-driven and built on a solid process comprehension.
Eliminate Quotas
Establishing numerical limitations might promote shortcuts while compromising quality. Organizations should prioritize assessing and improving the efficiency of processes over enforcing arbitrary quantity objectives.
Eliminate Barriers to Encourage Workmanship Pride
Supervisors’ responsibilities must shift away from raw numbers and toward quality. In many firms, hourly workers are treated as commodities. Such employees are always uncertain about their fate.
Encourage Self-Improvement
A business needs good personnel who are improving through education. Management should encourage everyone to further their education and pursue self-improvement.
Include Everyone in Pursuing Goals
The change is everyone’s responsibility. Management must take steps to complete the transition. To do this, there is a need to be aware that every task is part of an operation. A flow diagram that splits the procedure into stages may come in handy.
References
Metri, B. A. (2006). Total quality transportation through Deming’s 14 points. Journal of Public Transportation, 9(4), 35-46.
Sower, V. E., Quarles, R., & Broussard, E. (2007). Cost of quality usage and its relationship to quality system maturity. International Journal of Quality & Reliability Management, 24(2), 121–140. https://doi.org/10.1108/02656710710722257
ORDER A PLAGIARISM-FREE PAPER HERE
We’ll write everything from scratch
Question
In each assignment, you are to think critically about the topic and apply your knowledge. Analyze and just not summarize. Use APA headings for clarity and provide references as needed.
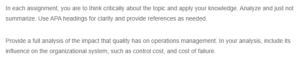
The Impact of Quality on Operations Management- Cost Control, Failure, and Organizational System Efficiency
Provide a full analysis of the impact that quality has on operations management. In your analysis, include its influence on the organizational system, such as control cost, and cost of failure.
Provide an analysis of Deming’s 14 Management Principles as they relate to quality. Be clear and focus on the application of the principles to quality control in an organization