The Case of the Variable Laminates
This paper covers the case study of a plywood manufacturer. The manufacturer is asking for assistance in solving a problem with its production. The production problem is the log-peeling process. The process consists of soaking debarked logs in a hot bath, fixing the records into chunks, and rapidly spinning them while shaving off a continuous thin section called a lamination with a sharp knife blade. The issue they are having is controlling the thickness when peeling laminations from a log. They use these laminations to create plywood sheets, and as of now, their product has thickness variations in them.
Upon investigation and speaking with engineers and process operators, it is determined that four variables are related to the thickness of the laminates. The variables are soak time, soak temperature, knife setting, and knife pressure. The problem was narrowed down to flow time, and the recommended soak time was sixty minutes. It was found that some laminates were being cut after the log had only been soaked for thirty minutes (Sower, 2011).
Designing an Experiment
The recommended soak time for the logs is sixty minutes. Having the logs soak for this exact amount of time is important to control the variation in thickness with the cuts. The company currently does not have control over this part of the process. The company must come up with a procedure for soaking that has balance, that is efficient, and that has a fit. To control this issue, the experiment that is designed should be a single-factor design.
A single-factor design focuses on one variable instead of all of the variables. It saves time and effort when addressing an issue with production. For this problem with the variation of thickness in laminates, there should be four test runs. Each test run should have a certain time limit. The wood is soaked before the peeling process is started.
Run Time | Time Soaked | Level of Thickness Achieved |
1 | 20 minutes | Yield |
2 | 30 minutes | Yield |
1 | 45 minutes | Yield |
2 | 60 minutes
Recommended time |
Yield |
By running these four tests, the plywood company can determine exactly how long their wood needs to be soaked for the desired thickness they want to achieve. After finding out the exact amount of time required to achieve the desired product thickness, it is my recommendation that the company implements a process in which they decide how many pieces they are going to soak at once and include a timer so that they can do their log-peeling process in batches and not as a continuous interval. Setting up a batch-time process will make it easier for the company to control every aspect of its production process.
The company’s concept of repeatable work was not at a high level. Repeatable work is when your company is able to produce the same product the same each time it is made. Because the company was unable to have the same thickness in each laminate because of an error in their process, I do not rate them high in repeatability. To standardize their approach, they should produce their laminates in batches. Batches of the product will have gone through the same treatment each time.
This means each batch will go through the same period of soaking and the same temperature when it is soaked. This allows control, and they can easily pinpoint when something is wrong with the length of time or temperature of the soak when a batch is not as how it should be. Repeatable work is very important. It is important because it shows the company that its operation process is going smoothly. If the company cannot repeat its job, then they are no longer able to compete with other companies who are able to produce the same quality over and over again.
References
Sower, V. E. (2011). Essentials of quality: With cases and experiential exercises.
Hoboken, NJ: John Wiley & Sons.
ORDER A PLAGIARISM-FREE PAPER HERE
We’ll write everything from scratch
Question
A plywood manufacturer has asked for your assistance in solving a problem in the log-peeling operation. The peeling process consists of soaking debarked logs in a hot bath, fixing the records in chunks, and rapidly spinning them while shaving off a continuous thin section called a lamination with a sharp knife blade. The laminations are then cut into sheets to be laid up, glued, and pressed into plywood sheets. The manufacturer is having difficulty maintaining a controlled thickness when peeling laminations from a log.
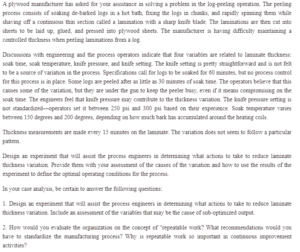
The Case of the Variable Laminates
Discussions with engineering and the process operators indicate that four variables are related to laminate thickness: soak time, soak temperature, knife pressure, and knife setting. The knife setting is pretty straightforward and is not felt to be a source of variation in the process. Specifications call for logs to be soaked for 60 minutes, but no process control for this process is in place. Some records are peeled after as little as 30 minutes of soak time. The operators believe that this causes some of the variation, but they are under the gun to keep the peeler busy, even if it means compromising on the soak time. The engineers feel that knife pressure may contribute to the thickness variation. The knife pressure setting is not standardized—operators set it between 250 psi and 300 psi based on their experience. Soak temperature varies between 150 degrees and 200 degrees, depending on how much bark has accumulated around the heating coils.
Thickness measurements are made every 15 minutes on the laminate. The variation does not seem to follow a particular pattern.
Design an experiment that will assist the process engineers in determining what actions to take to reduce laminate thickness variation. Please provide them with your assessment of the causes of the interpretation and how to use the results of the experiment to define the optimal operating conditions for the process.
In your case analysis, be certain to answer the following questions:
1. Design an experiment that will assist the process engineers in determining what actions to take to reduce laminate thickness variation. Include an assessment of the variables that may be the cause of sub-optimized output.
2. How would you evaluate the organization on the concept of “repeatable work? What recommendations would you have to standardize the manufacturing process? Why is repeatable work so important in continuous improvement activities?